How do you make your business grow? Experts tackle two tough questions.
Creating a Network
Question: I'm interested in build a network and gathering referrals. How is this done?
Answer:
Effective networking is more than just showing up at business mixers. Business owners who are outstanding networkers are systematic about the process. They create databases of people they know and their contact information, areas of interest and expertise and more. Then they establish ways to keep in touch.
Usually, they don't try to make immediate sales but seek to provide help. Many top networkers say they listen for problems their networking partners are experiencing. That's when people are ready to pat for help that they might not seek when things are going well.
Networks aren't built in a day
Building relationships takes time. You're not going to become a trusted friend, adviser and go-to buy overnight. So commit to the long haul.
Actually write time into your schedule to make calls to people in your network. Personal calls and e-mails are better for building relationships than bulk e-mails and newsletters.
Of course, the best way to maintain relationships is to do quality work and sell quality products. Few people will do business with nice people who are slipshod.
Saturday, November 18, 2006
Wednesday, November 15, 2006
我的未來不是夢? 台灣半導體設備本土化現況及未來
以南韓為借鏡,政府目前將LCD設備與關鍵零組件國產化列為產業政策重點項目。其中設備產業自製率的目標是2008年達到50%、產值朝新台幣630億元目標邁進,2010年以後維持自給率至少60%;而設備關鍵零組件自給率希望由2005年的20%提升至2008年 70%、產值達175億元之目標。
對照LCD設備產業,半導體設備本土化則是一路走來篳路藍縷,相較於工業局所公佈2005年台灣 LCD整體設備(含Array、Cell、Module、Inspection及Automation)自給率達21.96%,2005年台灣的半導體整體設備自給率還不到15%,一來一往之間,發展較久的半導體本土化是遠不如LCD本土化,然而問題在哪?業者與政府需做哪些方式因應呢?台灣半導體設備本土化現況及未來發展情形又會是如何呢?均將在下文討論之。
獨特的專業分工模式 引領台灣IC產業向前衝
台灣IC產業在歷經了30多年產、官、學、研界的共同努力下,目前實力在全球IC 產業已具備了一定的地位,2005年是僅次於美、日的全球第三大IC 生產國,IC產品產值達151億美元(約新台幣4,989億元)。台灣IC 產業與國外最大之不同點是在於專業分工的產業結構,因為在快速變遷的產業環境,以及與日漸增的擴大資本設備投資下,台灣獨特專業分工模式,比起國際大廠,相對地符合產業趨勢需求。
目前國際大廠多以設計、製造、封裝、測試,甚至系統產品等上、下游垂直整合的經營方式,然而台灣則是選擇採取上、下游垂直分工的經營型態,在集中資源於單一產業領域之術業專攻模式進行下,也確實獲得相當好的成效。
以台灣的專業分工體系來看,截至2005年底為止,台灣共有268家IC設計公司、8家晶圓材料業者、4家光罩公司、13家晶圓製造公司、33家封裝業者、35家測試業者、15家基板廠商、19家化學品廠商以及4家導線架生產廠商……等。
如此龐大且綿密的週邊相互支援廠商,讓台灣以1個虛擬上下整合產業鏈與其他國家競爭,設計部分,台灣設計業蓬勃發展,家數與產值(為新台幣3,200億元)皆僅次於美國;晶圓製造部分,晶圓製造業靠著晶圓雙雄在全球持續雄霸(2005年台灣晶圓代工市佔率72.4%)以及全球第二大的DRAM業者加持下,產值已達新台幣5,874億元;下游的封裝測試業也因上游優異的製造與代工能力,產值居於全球第一,為3,052億元。
就產品面而言,DRAM、SRAM等產品因進入市場較晚,已由美、日、韓等國佔取先機,但仍有第二的優異表現;Mask ROM則由於國外大廠接連退出,而使得台灣於近幾年皆獨佔全球第一的地位。
然而就在號稱是半導體王國的我們,12吋晶圓廠故鄉的口號下,晶圓製造的所需的關鍵設備的掌握度卻遠遠的落後其他先進國家(歐美日韓)。根據半導體協會SEMI統計,2006年半導體設備需求達388.1億美元,其中台灣地區超越南韓,達69.7億美元,位居全球第二。
看似美好龐大的市場,其實台灣業者大部分只能在後段封測設備(佔整體市場21%)上分得一杯羹,但是在前段關鍵製程設備,能夠有所發揮的業者卻少之又少(主要為漢民以及沛鑫2家業者)。
國產設備廠商切入主要市場 難難難
過去台灣半導體產業藉由國外大廠以及在製程與設備技術轉移下,產業快速成長,尤其台灣在半導體代工模式發展下掌握了成本競爭力,與國際大廠合作開發製程更逐漸累積先進技術優勢,在全球半導體產業分工下,台灣半導體代工產業對於龐大的設備需求十分旺盛。然而這麼大的設備需求,台灣不僅整體設備自製率不到 15%(前段設備僅達5%左右),連關鍵材料的掌握也都受制於國外廠商,連帶造成產業鏈發展不均衡,廠商議價能力也因此受到拘束。
這對於台灣而言,等於是將每年1,000多億元的市場拱手讓給國外大廠,也因此政府也開始重視與積極推動半導體設備產業的發展,為避免研發經費過於龐大,業者無法負擔,使用獎勵投資方案,利用科專與國科會計畫支持下發展許多半導體生產設備技術,且陸續由台灣研究單位(工研院、中科院)移轉至設備廠商,但往往因為推出時程,以及技術無法符合台灣製造業者需求遭到失敗的命運。
這是因為在高階製程設備需求方面,半導體製程發展快速,線寬也不斷朝向物理、化學、光學的極限前進,由於設備研發面對的困難度倍增,研發金額急遽上升,設備售價格更是不斷向上攀升,因此高階製程(如0.13微米以下製程)設備通常搭配12吋晶圓增加設備產出,藉以提高單一設備效益。
也正因為1片12吋晶圓產出晶粒數為8吋晶圓的2.25倍,因此12吋設備已成半導體廠主要的購置設備,但相對地有能力建廠的業者卻變少(1座12吋廠需要20億∼25億美元),連帶造成12吋設備需求數量較過去8吋廠為低,僧多(設備業者)粥少(設備需求)情況下,台灣設備業者不見得可以進入製造業者評估範圍內。
縱使台灣設備業者以設備低廉為主打,製造業者也不會因此就會購買,因為半導體產品變化速度極快,隨著新產品的出現及製程技術的提升,有時舊有設備必須完全淘汰,研製全新設備方能符合市場要求,例如隨製程技術邁向90奈米主流的同時,化學機械研磨機、覆晶封裝就成為市場主流,另隨著銅製程技術的進步,許多設備開發皆需隨之調整。
而半導體製造材料昂貴,任何製程中的疏失都將造成無可彌補的巨大損失,因此製造設備的可靠度及精密度要求成為必要條件,即使台灣在精密機械加工技術層次有相當水準,所開發出的設備仍很難獲得市場接受。
當然也有台灣設備業者採取先推機台讓製造廠商試用,等到廠商確定設備沒問題後再行購買,但是以前段製程設備單一設備上千萬的金額,再加上量產前龐大的研費經費支出,台灣設備業者除了少數擁有雄厚資金的幾家業者,能夠有足夠資金一次生產好幾台設備,置放在不同的客戶廠房內生產,並試用到滿意付款外,剩下的幾乎只能轉到成熟且風險性較低的設備,畢竟這一試用下去,就不知道何時才能回收。
台灣前後段製程設備國產化5階段時期回顧
其實以台灣每年台灣超過新台幣1,000億元內需市場,配合台灣半導體產業投資發展計畫,幾乎可以讓台灣成為亞太地區設備研發與製造中心,供應東南亞以及大陸市場。就台灣半導體設備產業發展分析,屬於半導體後段製程的封裝技術較為成熟,至於前段製程設備僅有少數幾家業者有能力。
台灣早期的封裝設備是由外商的封裝廠自動化部門自行開發生產製造,不過隨著封裝廠人力向四處擴散且一些台灣廠商先後加入後段封裝設備製造,逐漸帶動封裝設備產業國產化製造蓬勃發展,而這些業者早期的設備,是切入屬於封裝後段Trim/Form設備與模具耗材部分,最後才逐漸轉往生產自動蓋印設備,這一階段時期約為 1980年代。
之後政府由科專計劃委託研發單位如工研院機械所等,引進封裝前段關鍵製程技術,包含晶圓切割、黏晶、銲線等關鍵製程技術,而設備廠商在發展上也由當初利基型設備累積技術,逐漸轉往關鍵製程設備的開發,此時政府也在1995年成立「精密機械工業發展推動小組」,藉此推動協助廠商半導體設備國產化。
當時台灣切入後段封裝設備業者包含:晶圓切割設備、BGA切割設備的優力特公司;黏晶、晶粒取放設備的廠商均豪精密與斯利康科技;生產Trim/Form設備的廠商為基丞、鉅基與盛技科技等;基板清洗設備、蓋印設備鈦昇科技;蓋印設備的格瑞科技;生產基板清洗設備的廠商則為暉聖科技。
而廠商也開發出新設備包含:均豪精密的自動封膠設備與覆晶黏晶設備;鈦昇科技的Plasma BGA基板清洗設備,並與封裝大廠共同研發覆晶製程相關設備,以當時技術而言,雖然許多台灣業者在前段設備並沒有有所發揮,但在後段封測設備部分,卻是大步向前加快腳步追趕,也讓一些後段製程設備技術上已逐漸縮小與國外大廠的技術差距。
1996年政府將半導體設備國產化列為10大新興工業之一,並訂定「新興重要策略性產業獎勵辦法」項目,希望藉此輔佐國產半導體前後段製程設備國產化。與前2階段不同的,這一段不是由純國產設備製造商主導,而是由另外二種類型業者帶領國產製程設備向前衝,第一種是代理商轉型,第二種則是歸國學人創業,至於業者有:黏晶設備的華東半導體;電漿(Plasma)廠商晶研科技;後段測試的蔚華系統……等。
時序進入2000年,由於台灣設備需求量龐大,隨著台灣加工能力提昇,國外設備廠商(主要是美商應用材料)開始萌生零組件當地供應的策略,希望一方面降低零組件成本,另一方面則是希望藉由零組件當地供應策略縮短交期、減少庫存與備料,因此產生半導體設備零組件委外製造的商機。
在前段零組件、半導體設備的耗材如Qauds、Rings等產品上,已有包括慶康、啟成、日揚等廠商已進行開發生產;至於在腔體的製造與處理上,已涉入或少量進行實驗設備組件代工的廠商包含如公準、日揚、榮眾等廠商。
然而相較於後段封測設備一堆業者如火如荼紛紛加入,前段製程設備則是在發展上則遭遇較大的挑戰,雖然當時台灣晶圓製造技術與製程能力已經逐漸趕上國際水準,但畢竟台灣前段製程設備起步較晚,相對地在製程能力累積不足,再加上國外設備大廠技術開發資金上之投入,台灣廠商的研發資源相對是比較薄弱。
此時台灣加入半導體前段製程設備生產的業者包括:弘塑科技與崧展科技則是發展濕製程清洗設備;生產沉積、蝕刻設備的廠商倍強真空;而從和立聯合真空部門獨立出來的中華聯合半導體,則是購併YAC在台之子公司台科半導體,生產製造凸塊UBM用真空濺鍍設備、高密度電漿機台;以電漿技術為核心,發展電漿蝕刻設備、PECVD等設備的晶研科技。
而在這階段,有1個跟前3階段不一樣的情形,那就是大型企業轉投資進入半導體設備代工行列,包括鴻海、東元集團、大同等廠商相繼跨行投資半導體設備製造相關領域,尤其是對於模組與次系統的代工相當積極,逐漸改變台灣半導體設備產業的生態。
包括沛鑫半導體挾鴻海在精密加工上的優勢,與應用材料、Anelva等廠商合作;東元集團專注於包含伺服馬達等產品,曾與南韓周星洽談合作;至於大同公司則是希望以其重電領域的經驗與優勢,切入半導體設備配電系統的相關領域。
至於第五階段的發展,算是台灣發展半導體前段設備,甚至於是擺脫代工設備製造,改以自有品牌設備銷售豐收的時候,包括崇越由代理國外半導體設備起家,再切入二手設備與零組件代工,近來也推出自有品牌產品;帆宣主要為系統代理廠商,目前並自行生產零組件,且跨足生產平面顯示器設備;購併電漿廠商晶研科技,營運資金2.1億元。
成功開發出反應離子蝕刻機(RIE)、電漿輔助化學氣相沉積(PECVD)、高密度電漿蝕刻機(HDP- Etcher)、電漿清潔及改質機(PRS系列)等多種量產用電漿真空設備晶研科技併入志聖工業,成為志聖工業竹科分公司;曾購併華東半導體的均豪精密,也順利合併群錄自動化,合併後的均豪集團,將發展為3個事業群,原群錄自動化則改為均豪精密中科群錄分公司,;蔚華科與設備原廠科頓(Credence)合資成立科頓蔚華技術整合公司,實收資本額新台幣1,800萬元,總部設於新竹,並於高雄設有營運據點。
然而最成功的應屬代理商漢民系統,轉投資漢民微測及漢辰科技,切入缺陷量測(Defect Inspection)及離子佈值(Ion Implant),並推出自有品牌設備,除了已經順利銷售到台積電、聯電、茂德等台灣晶圓製造業者外,也順利外銷到其他地區(北美、日本、新加坡等),替台灣本土半導體前段製程設備技術扳回一成。
機會在哪? 跨越障礙往前衝
至於本土國產設備業者在前段設備還有哪些商機呢?主要可以分為整機以及零組件、耗材兩部分。整機代工部分,比起TFT LCD產業,台灣能夠著墨的地方還是有限,因為國外半導體設備商未來勢必面臨降低成本的壓力,但畢竟在台生產並沒有迫切性,導致多數國外設備業者整機在台灣生產的意願極低。
以TFT LCD產業來講,每一世代進化,生產用設備機台尺寸相對暴增, 如友達在2005年向Applied Films(現已被應用材料購併)訂購的六代線尺寸用於彩色濾光片製程用的ITO真空濺鍍機台體積龐大,整個機台尺寸長達40公尺、寬10公尺,總重 170噸。
最後動用安托諾夫AN-225及華航B747-400全貨機各1架,前者載運15箱140噸重機台,後者載運19箱30噸重機台。設備抵台後,友達共準備18輛拖板車擔任陸上運輸,其陸上運輸車隊長達1.5公里,再全程由高速公路警察護送自二號國道轉一號國道,直接送至中科友達光電六代廠。
反觀12吋半導體製程設備尺寸再怎麼大,也不需要動用到如何龐大的資源,再加上考量到其他因素(台灣整機製造能力、原廠技術外流、資金等等),所以除了少數1∼2家業者(如沛鑫等)有機會替國外設備大廠代工整機外,恐怕台灣設備業者現階段能夠接單生產的,恐怕還是集中在零組件、耗材如Qauds、Rings等產品。
以應用材料為例,台灣製造中心所生產的各模組,包括潔淨室製造用的晶圓平邊對準室(Orienter Chamber)、晶圓冷卻室(Cooldown Chamber)以及電漿調節器(DPS RF、MatchRF、MatchHE RF Match)、除氣裝置(PVD Degas)晶圓承載器(P5000 LiftPVD HP Lift)等有超過50%的零件,包括金屬零組件、石英零組件、矽材料零組件、陶瓷零組件、石墨零組件、PCB、線束(cable harness)等都在台灣採購。
但不要小看零組件、半導體設備的耗材技術深度及市場,使用這些半導體機械設備必會產生磨耗,因此定期更換耗材是維持機器正常運轉所必須的程序步驟。然而半導體用零組件、耗材多使用於真空腔體環境中,然而在真空過程中,零組件材料組織內外,常會釋出對製程反應具不良影響或會破壞腔體真空度、潔淨度的氣體分子、水氣及不純物,最後會導致晶圓品質受損,而造成各種瑕疵產生。
對於晶圓製造業者而言,也希望這些用於前段設備零組件、耗材市場都能國產化,以一個簡易公式來看,零組件總成本=採購成本+庫存管理成本+機會成本,單單在採購成本這一項目上,台灣跟國外生產一來一往就有關稅差距,這還不包括交期時間、製程變動不夠彈性等問題,由此可知前段設備零組件、耗材國產化對於降低成本的重要性。
至於在市場方面,根據應用材料統計,2005年全球前段製程設備市場約為240億美元,但用於前段設備零組件、耗材市場就達90億美元,若單純計算台灣的市場值,也有將近14億美元,不可謂不多,更何況這些前段設備零組件、耗材市場是年年都有需求,不是可以用一輩子;再加上設備業者可以利用生產零組件練兵,藉此厚植實力,替日後整機代工做準備。
發展台灣半導體設備本土化優劣勢分析
當然只看市場多大是劃地自限,而是應該要先檢視自我優劣勢,補強不足,發揮所長,才能夠有機會爭取到每年新台幣上千億元的市場。將分以下5個部分討論之,包括系統機電整合能力、特殊製程技術能力、品質管理系統能否達到跨國企業的要求、全球運籌管理能力、公司財務能否承擔半導體產業景氣循環的考驗。
首先是在系統機電整合能力上,系統機電整合包含了自動化系統,機電產品製程技術,機械視覺,機電介面與系統整合,電腦及週邊設備等領域結合,但相較於國外,雖然台灣學校體系培養出許多相關專業人才,但這些人才往往是系統機電整合能力擁有部分強項,但其中1∼2項則是較為欠缺或是薄弱(如懂機械的,電機方面較為薄弱)。
接著則是特殊製程技術能力,台灣設備製造業者不是單純只有製造1台設備如此簡單,其公司在半導體製程方面的能力,必須能夠符合晶圓製造業者需求,且能適應半導體快速進展必須不斷研發的產業生態,因為晶圓製造業者往往會依照客戶需求,而有一些製程上改變,倘若設備製造業者對此方面技術能力不夠,即使一開始可以將設備銷售出去,但未來恐怕仍會遭到淘汰命運。
第三點則是品質系統管理上,這一點往往是與跨國企業合作的門檻,這一點主要是標榜透過品質系統管理(如ISO 9001為例)驗證,將使其組織架構更為精簡、整體表現更優異,更容易掌握公司的發展狀況,使得在日益競爭的全球市場上,更有實力佔得先機。
其次為全球運籌管理能力。運籌(logistics),較通俗的講法為物流,其在1920年代的原始定義為實體分配,如運輸和儲存,以及較優越的行銷手法;1980年代中整合性物流興起,重視透過加值供應鏈,適時、適地與適量地將高品質的產品送到顧客手中;而1990年代更醞釀了策略性物流(strategic logistics)的概念,著重於利用通路夥伴聯盟與物流能力來爭取競爭優勢;現階段則是強調接單後生產(Build-to-order;BTO)為主的新營運策略。
最後則是公司財務方面,以美歐半導體設備先進國家的設備商為例,首先是應用材料,2005年(會計年度)營收為 69.91億美元,研發(R&D)費用則是9.41億美元,佔整體營收為13.5%。至於微影設備大廠ASML,2005年(會計年度)營收為 25.29億歐元,研發費用則是3.24億美元,佔整體營收為12.8%。單單這兩家公司花在研發上面的金額以及佔營收比例之高,恐怕已經沒有幾家本土半導體設備業者可以負擔。
看看競爭者政策制訂 回頭想想該如何應對
往前看領先者(歐美日3個競爭者),如何趕上他們的確是刻不容緩的事,但是如何避免競爭者(南韓、大陸)追上也重要課題,因此檢視主要競爭者國家的政策制訂,希望能夠藉此給政府部門參考,並考慮應變對策。
在南韓部分,南韓政府計劃於2007∼2015年間以每3年一階段方式,分3期投入3,600億韓元的研發經費,推動半導體設備國產化,未來並將設立半導體核心設備開發準備委員會,研發半導體用光罩蝕刻設備、光罩用鍍膜設備、Neutral Beam設備等實用裝備,以及步進機等下一代核心設備,並確保根源技術。
而這3階段的經費分配分別為900億韓元(每年300億韓元)、1,200億韓元(每年400億韓元)、1,500億韓元(每年500億韓元),並將設立相對基金(Matching fund),提供設備業者及元件業者研發支援。
目前南韓半導體設備國產化的程度不及20%,但為了要在2015年達成國產化50%的目標,南韓政府亦制定了「2015半導體發展策略」,推動半導體設備國產化。包括三星電子(Samsung)、海力士(Hynix)、東部亞南(DongbuAnam)半導體等主要業者及學界、研究機構、政府等單位,也將於2007年正式推動「半導體核心設備開發事業團」。
至於大陸部分,隨著第十一次5年計畫(2006∼2010)的啟動,發展主軸為提高技術層次並擴及半導體材料與設備領域,其次則是新增「積體電路產業促進條例」,根據資訊產業科技發展「十一五」規劃和2020年中長期規劃綱要,半導體技術獎勵政策,初步決定將以12吋廠與0.18微米以下先進製程為主,改變以往全面性的獎勵方式,重點發展項目包括12吋晶圓廠、16吋晶圓廠以及90奈米、65奈米和45奈米製程技術、MEMS技術、新型、高密度積體電路封裝、測試技術。
而在國產化設備部分,獎勵部分則為半導體和積體電路專用設備製造技術(含矽基、化合物、寬禁帶半導體設備製造技術)以及半導體和積體電路測試儀器製造技術,目標是6吋晶圓生產線設備上完全自主,8吋晶圓以及12吋晶圓生產線0.13∼0.065微米微影設備等有所突破。
且新的半導體產業發展政策除對半導體業者採行「五免五減半」的所得稅優惠措施外,另提供業者研發減稅、半導體設備支出免稅,以及協助IC設計業者尋求資金籌措管道等;並計劃成立專案基金扶植半導體產業,第一年基金規模達1,200萬∼2,500萬美元,之後基金規模將逐年擴大。
台灣在半導體產業中佔有不可替代的重要地位,如何利用既有的優勢來帶動半導體次產業(設備、材料等)的興起,是相關廠商以及政府部門所必須重視的。面對南韓強力競爭與大陸半導體產業日益蓬勃發展的威脅,台灣政府部門應該思考如何協助業者能夠創新技術,掌握半導體設備發展,讓不僅晶圓生產技術根留台灣,同時設備方面也能自主,厚植台灣半導體產業基礎技術,補足長久一來,台灣所欠缺的這一塊空白。
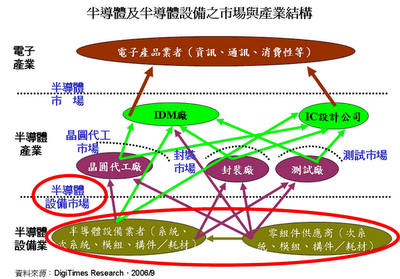
對照LCD設備產業,半導體設備本土化則是一路走來篳路藍縷,相較於工業局所公佈2005年台灣 LCD整體設備(含Array、Cell、Module、Inspection及Automation)自給率達21.96%,2005年台灣的半導體整體設備自給率還不到15%,一來一往之間,發展較久的半導體本土化是遠不如LCD本土化,然而問題在哪?業者與政府需做哪些方式因應呢?台灣半導體設備本土化現況及未來發展情形又會是如何呢?均將在下文討論之。
獨特的專業分工模式 引領台灣IC產業向前衝
台灣IC產業在歷經了30多年產、官、學、研界的共同努力下,目前實力在全球IC 產業已具備了一定的地位,2005年是僅次於美、日的全球第三大IC 生產國,IC產品產值達151億美元(約新台幣4,989億元)。台灣IC 產業與國外最大之不同點是在於專業分工的產業結構,因為在快速變遷的產業環境,以及與日漸增的擴大資本設備投資下,台灣獨特專業分工模式,比起國際大廠,相對地符合產業趨勢需求。
目前國際大廠多以設計、製造、封裝、測試,甚至系統產品等上、下游垂直整合的經營方式,然而台灣則是選擇採取上、下游垂直分工的經營型態,在集中資源於單一產業領域之術業專攻模式進行下,也確實獲得相當好的成效。
以台灣的專業分工體系來看,截至2005年底為止,台灣共有268家IC設計公司、8家晶圓材料業者、4家光罩公司、13家晶圓製造公司、33家封裝業者、35家測試業者、15家基板廠商、19家化學品廠商以及4家導線架生產廠商……等。
如此龐大且綿密的週邊相互支援廠商,讓台灣以1個虛擬上下整合產業鏈與其他國家競爭,設計部分,台灣設計業蓬勃發展,家數與產值(為新台幣3,200億元)皆僅次於美國;晶圓製造部分,晶圓製造業靠著晶圓雙雄在全球持續雄霸(2005年台灣晶圓代工市佔率72.4%)以及全球第二大的DRAM業者加持下,產值已達新台幣5,874億元;下游的封裝測試業也因上游優異的製造與代工能力,產值居於全球第一,為3,052億元。
就產品面而言,DRAM、SRAM等產品因進入市場較晚,已由美、日、韓等國佔取先機,但仍有第二的優異表現;Mask ROM則由於國外大廠接連退出,而使得台灣於近幾年皆獨佔全球第一的地位。
然而就在號稱是半導體王國的我們,12吋晶圓廠故鄉的口號下,晶圓製造的所需的關鍵設備的掌握度卻遠遠的落後其他先進國家(歐美日韓)。根據半導體協會SEMI統計,2006年半導體設備需求達388.1億美元,其中台灣地區超越南韓,達69.7億美元,位居全球第二。
看似美好龐大的市場,其實台灣業者大部分只能在後段封測設備(佔整體市場21%)上分得一杯羹,但是在前段關鍵製程設備,能夠有所發揮的業者卻少之又少(主要為漢民以及沛鑫2家業者)。
國產設備廠商切入主要市場 難難難
過去台灣半導體產業藉由國外大廠以及在製程與設備技術轉移下,產業快速成長,尤其台灣在半導體代工模式發展下掌握了成本競爭力,與國際大廠合作開發製程更逐漸累積先進技術優勢,在全球半導體產業分工下,台灣半導體代工產業對於龐大的設備需求十分旺盛。然而這麼大的設備需求,台灣不僅整體設備自製率不到 15%(前段設備僅達5%左右),連關鍵材料的掌握也都受制於國外廠商,連帶造成產業鏈發展不均衡,廠商議價能力也因此受到拘束。
這對於台灣而言,等於是將每年1,000多億元的市場拱手讓給國外大廠,也因此政府也開始重視與積極推動半導體設備產業的發展,為避免研發經費過於龐大,業者無法負擔,使用獎勵投資方案,利用科專與國科會計畫支持下發展許多半導體生產設備技術,且陸續由台灣研究單位(工研院、中科院)移轉至設備廠商,但往往因為推出時程,以及技術無法符合台灣製造業者需求遭到失敗的命運。
這是因為在高階製程設備需求方面,半導體製程發展快速,線寬也不斷朝向物理、化學、光學的極限前進,由於設備研發面對的困難度倍增,研發金額急遽上升,設備售價格更是不斷向上攀升,因此高階製程(如0.13微米以下製程)設備通常搭配12吋晶圓增加設備產出,藉以提高單一設備效益。
也正因為1片12吋晶圓產出晶粒數為8吋晶圓的2.25倍,因此12吋設備已成半導體廠主要的購置設備,但相對地有能力建廠的業者卻變少(1座12吋廠需要20億∼25億美元),連帶造成12吋設備需求數量較過去8吋廠為低,僧多(設備業者)粥少(設備需求)情況下,台灣設備業者不見得可以進入製造業者評估範圍內。
縱使台灣設備業者以設備低廉為主打,製造業者也不會因此就會購買,因為半導體產品變化速度極快,隨著新產品的出現及製程技術的提升,有時舊有設備必須完全淘汰,研製全新設備方能符合市場要求,例如隨製程技術邁向90奈米主流的同時,化學機械研磨機、覆晶封裝就成為市場主流,另隨著銅製程技術的進步,許多設備開發皆需隨之調整。
而半導體製造材料昂貴,任何製程中的疏失都將造成無可彌補的巨大損失,因此製造設備的可靠度及精密度要求成為必要條件,即使台灣在精密機械加工技術層次有相當水準,所開發出的設備仍很難獲得市場接受。
當然也有台灣設備業者採取先推機台讓製造廠商試用,等到廠商確定設備沒問題後再行購買,但是以前段製程設備單一設備上千萬的金額,再加上量產前龐大的研費經費支出,台灣設備業者除了少數擁有雄厚資金的幾家業者,能夠有足夠資金一次生產好幾台設備,置放在不同的客戶廠房內生產,並試用到滿意付款外,剩下的幾乎只能轉到成熟且風險性較低的設備,畢竟這一試用下去,就不知道何時才能回收。
台灣前後段製程設備國產化5階段時期回顧
其實以台灣每年台灣超過新台幣1,000億元內需市場,配合台灣半導體產業投資發展計畫,幾乎可以讓台灣成為亞太地區設備研發與製造中心,供應東南亞以及大陸市場。就台灣半導體設備產業發展分析,屬於半導體後段製程的封裝技術較為成熟,至於前段製程設備僅有少數幾家業者有能力。
台灣早期的封裝設備是由外商的封裝廠自動化部門自行開發生產製造,不過隨著封裝廠人力向四處擴散且一些台灣廠商先後加入後段封裝設備製造,逐漸帶動封裝設備產業國產化製造蓬勃發展,而這些業者早期的設備,是切入屬於封裝後段Trim/Form設備與模具耗材部分,最後才逐漸轉往生產自動蓋印設備,這一階段時期約為 1980年代。
之後政府由科專計劃委託研發單位如工研院機械所等,引進封裝前段關鍵製程技術,包含晶圓切割、黏晶、銲線等關鍵製程技術,而設備廠商在發展上也由當初利基型設備累積技術,逐漸轉往關鍵製程設備的開發,此時政府也在1995年成立「精密機械工業發展推動小組」,藉此推動協助廠商半導體設備國產化。
當時台灣切入後段封裝設備業者包含:晶圓切割設備、BGA切割設備的優力特公司;黏晶、晶粒取放設備的廠商均豪精密與斯利康科技;生產Trim/Form設備的廠商為基丞、鉅基與盛技科技等;基板清洗設備、蓋印設備鈦昇科技;蓋印設備的格瑞科技;生產基板清洗設備的廠商則為暉聖科技。
而廠商也開發出新設備包含:均豪精密的自動封膠設備與覆晶黏晶設備;鈦昇科技的Plasma BGA基板清洗設備,並與封裝大廠共同研發覆晶製程相關設備,以當時技術而言,雖然許多台灣業者在前段設備並沒有有所發揮,但在後段封測設備部分,卻是大步向前加快腳步追趕,也讓一些後段製程設備技術上已逐漸縮小與國外大廠的技術差距。
1996年政府將半導體設備國產化列為10大新興工業之一,並訂定「新興重要策略性產業獎勵辦法」項目,希望藉此輔佐國產半導體前後段製程設備國產化。與前2階段不同的,這一段不是由純國產設備製造商主導,而是由另外二種類型業者帶領國產製程設備向前衝,第一種是代理商轉型,第二種則是歸國學人創業,至於業者有:黏晶設備的華東半導體;電漿(Plasma)廠商晶研科技;後段測試的蔚華系統……等。
時序進入2000年,由於台灣設備需求量龐大,隨著台灣加工能力提昇,國外設備廠商(主要是美商應用材料)開始萌生零組件當地供應的策略,希望一方面降低零組件成本,另一方面則是希望藉由零組件當地供應策略縮短交期、減少庫存與備料,因此產生半導體設備零組件委外製造的商機。
在前段零組件、半導體設備的耗材如Qauds、Rings等產品上,已有包括慶康、啟成、日揚等廠商已進行開發生產;至於在腔體的製造與處理上,已涉入或少量進行實驗設備組件代工的廠商包含如公準、日揚、榮眾等廠商。
然而相較於後段封測設備一堆業者如火如荼紛紛加入,前段製程設備則是在發展上則遭遇較大的挑戰,雖然當時台灣晶圓製造技術與製程能力已經逐漸趕上國際水準,但畢竟台灣前段製程設備起步較晚,相對地在製程能力累積不足,再加上國外設備大廠技術開發資金上之投入,台灣廠商的研發資源相對是比較薄弱。
此時台灣加入半導體前段製程設備生產的業者包括:弘塑科技與崧展科技則是發展濕製程清洗設備;生產沉積、蝕刻設備的廠商倍強真空;而從和立聯合真空部門獨立出來的中華聯合半導體,則是購併YAC在台之子公司台科半導體,生產製造凸塊UBM用真空濺鍍設備、高密度電漿機台;以電漿技術為核心,發展電漿蝕刻設備、PECVD等設備的晶研科技。
而在這階段,有1個跟前3階段不一樣的情形,那就是大型企業轉投資進入半導體設備代工行列,包括鴻海、東元集團、大同等廠商相繼跨行投資半導體設備製造相關領域,尤其是對於模組與次系統的代工相當積極,逐漸改變台灣半導體設備產業的生態。
包括沛鑫半導體挾鴻海在精密加工上的優勢,與應用材料、Anelva等廠商合作;東元集團專注於包含伺服馬達等產品,曾與南韓周星洽談合作;至於大同公司則是希望以其重電領域的經驗與優勢,切入半導體設備配電系統的相關領域。
至於第五階段的發展,算是台灣發展半導體前段設備,甚至於是擺脫代工設備製造,改以自有品牌設備銷售豐收的時候,包括崇越由代理國外半導體設備起家,再切入二手設備與零組件代工,近來也推出自有品牌產品;帆宣主要為系統代理廠商,目前並自行生產零組件,且跨足生產平面顯示器設備;購併電漿廠商晶研科技,營運資金2.1億元。
成功開發出反應離子蝕刻機(RIE)、電漿輔助化學氣相沉積(PECVD)、高密度電漿蝕刻機(HDP- Etcher)、電漿清潔及改質機(PRS系列)等多種量產用電漿真空設備晶研科技併入志聖工業,成為志聖工業竹科分公司;曾購併華東半導體的均豪精密,也順利合併群錄自動化,合併後的均豪集團,將發展為3個事業群,原群錄自動化則改為均豪精密中科群錄分公司,;蔚華科與設備原廠科頓(Credence)合資成立科頓蔚華技術整合公司,實收資本額新台幣1,800萬元,總部設於新竹,並於高雄設有營運據點。
然而最成功的應屬代理商漢民系統,轉投資漢民微測及漢辰科技,切入缺陷量測(Defect Inspection)及離子佈值(Ion Implant),並推出自有品牌設備,除了已經順利銷售到台積電、聯電、茂德等台灣晶圓製造業者外,也順利外銷到其他地區(北美、日本、新加坡等),替台灣本土半導體前段製程設備技術扳回一成。
機會在哪? 跨越障礙往前衝
至於本土國產設備業者在前段設備還有哪些商機呢?主要可以分為整機以及零組件、耗材兩部分。整機代工部分,比起TFT LCD產業,台灣能夠著墨的地方還是有限,因為國外半導體設備商未來勢必面臨降低成本的壓力,但畢竟在台生產並沒有迫切性,導致多數國外設備業者整機在台灣生產的意願極低。
以TFT LCD產業來講,每一世代進化,生產用設備機台尺寸相對暴增, 如友達在2005年向Applied Films(現已被應用材料購併)訂購的六代線尺寸用於彩色濾光片製程用的ITO真空濺鍍機台體積龐大,整個機台尺寸長達40公尺、寬10公尺,總重 170噸。
最後動用安托諾夫AN-225及華航B747-400全貨機各1架,前者載運15箱140噸重機台,後者載運19箱30噸重機台。設備抵台後,友達共準備18輛拖板車擔任陸上運輸,其陸上運輸車隊長達1.5公里,再全程由高速公路警察護送自二號國道轉一號國道,直接送至中科友達光電六代廠。
反觀12吋半導體製程設備尺寸再怎麼大,也不需要動用到如何龐大的資源,再加上考量到其他因素(台灣整機製造能力、原廠技術外流、資金等等),所以除了少數1∼2家業者(如沛鑫等)有機會替國外設備大廠代工整機外,恐怕台灣設備業者現階段能夠接單生產的,恐怕還是集中在零組件、耗材如Qauds、Rings等產品。
以應用材料為例,台灣製造中心所生產的各模組,包括潔淨室製造用的晶圓平邊對準室(Orienter Chamber)、晶圓冷卻室(Cooldown Chamber)以及電漿調節器(DPS RF、MatchRF、MatchHE RF Match)、除氣裝置(PVD Degas)晶圓承載器(P5000 LiftPVD HP Lift)等有超過50%的零件,包括金屬零組件、石英零組件、矽材料零組件、陶瓷零組件、石墨零組件、PCB、線束(cable harness)等都在台灣採購。
但不要小看零組件、半導體設備的耗材技術深度及市場,使用這些半導體機械設備必會產生磨耗,因此定期更換耗材是維持機器正常運轉所必須的程序步驟。然而半導體用零組件、耗材多使用於真空腔體環境中,然而在真空過程中,零組件材料組織內外,常會釋出對製程反應具不良影響或會破壞腔體真空度、潔淨度的氣體分子、水氣及不純物,最後會導致晶圓品質受損,而造成各種瑕疵產生。
對於晶圓製造業者而言,也希望這些用於前段設備零組件、耗材市場都能國產化,以一個簡易公式來看,零組件總成本=採購成本+庫存管理成本+機會成本,單單在採購成本這一項目上,台灣跟國外生產一來一往就有關稅差距,這還不包括交期時間、製程變動不夠彈性等問題,由此可知前段設備零組件、耗材國產化對於降低成本的重要性。
至於在市場方面,根據應用材料統計,2005年全球前段製程設備市場約為240億美元,但用於前段設備零組件、耗材市場就達90億美元,若單純計算台灣的市場值,也有將近14億美元,不可謂不多,更何況這些前段設備零組件、耗材市場是年年都有需求,不是可以用一輩子;再加上設備業者可以利用生產零組件練兵,藉此厚植實力,替日後整機代工做準備。
發展台灣半導體設備本土化優劣勢分析
當然只看市場多大是劃地自限,而是應該要先檢視自我優劣勢,補強不足,發揮所長,才能夠有機會爭取到每年新台幣上千億元的市場。將分以下5個部分討論之,包括系統機電整合能力、特殊製程技術能力、品質管理系統能否達到跨國企業的要求、全球運籌管理能力、公司財務能否承擔半導體產業景氣循環的考驗。
首先是在系統機電整合能力上,系統機電整合包含了自動化系統,機電產品製程技術,機械視覺,機電介面與系統整合,電腦及週邊設備等領域結合,但相較於國外,雖然台灣學校體系培養出許多相關專業人才,但這些人才往往是系統機電整合能力擁有部分強項,但其中1∼2項則是較為欠缺或是薄弱(如懂機械的,電機方面較為薄弱)。
接著則是特殊製程技術能力,台灣設備製造業者不是單純只有製造1台設備如此簡單,其公司在半導體製程方面的能力,必須能夠符合晶圓製造業者需求,且能適應半導體快速進展必須不斷研發的產業生態,因為晶圓製造業者往往會依照客戶需求,而有一些製程上改變,倘若設備製造業者對此方面技術能力不夠,即使一開始可以將設備銷售出去,但未來恐怕仍會遭到淘汰命運。
第三點則是品質系統管理上,這一點往往是與跨國企業合作的門檻,這一點主要是標榜透過品質系統管理(如ISO 9001為例)驗證,將使其組織架構更為精簡、整體表現更優異,更容易掌握公司的發展狀況,使得在日益競爭的全球市場上,更有實力佔得先機。
其次為全球運籌管理能力。運籌(logistics),較通俗的講法為物流,其在1920年代的原始定義為實體分配,如運輸和儲存,以及較優越的行銷手法;1980年代中整合性物流興起,重視透過加值供應鏈,適時、適地與適量地將高品質的產品送到顧客手中;而1990年代更醞釀了策略性物流(strategic logistics)的概念,著重於利用通路夥伴聯盟與物流能力來爭取競爭優勢;現階段則是強調接單後生產(Build-to-order;BTO)為主的新營運策略。
最後則是公司財務方面,以美歐半導體設備先進國家的設備商為例,首先是應用材料,2005年(會計年度)營收為 69.91億美元,研發(R&D)費用則是9.41億美元,佔整體營收為13.5%。至於微影設備大廠ASML,2005年(會計年度)營收為 25.29億歐元,研發費用則是3.24億美元,佔整體營收為12.8%。單單這兩家公司花在研發上面的金額以及佔營收比例之高,恐怕已經沒有幾家本土半導體設備業者可以負擔。
看看競爭者政策制訂 回頭想想該如何應對
往前看領先者(歐美日3個競爭者),如何趕上他們的確是刻不容緩的事,但是如何避免競爭者(南韓、大陸)追上也重要課題,因此檢視主要競爭者國家的政策制訂,希望能夠藉此給政府部門參考,並考慮應變對策。
在南韓部分,南韓政府計劃於2007∼2015年間以每3年一階段方式,分3期投入3,600億韓元的研發經費,推動半導體設備國產化,未來並將設立半導體核心設備開發準備委員會,研發半導體用光罩蝕刻設備、光罩用鍍膜設備、Neutral Beam設備等實用裝備,以及步進機等下一代核心設備,並確保根源技術。
而這3階段的經費分配分別為900億韓元(每年300億韓元)、1,200億韓元(每年400億韓元)、1,500億韓元(每年500億韓元),並將設立相對基金(Matching fund),提供設備業者及元件業者研發支援。
目前南韓半導體設備國產化的程度不及20%,但為了要在2015年達成國產化50%的目標,南韓政府亦制定了「2015半導體發展策略」,推動半導體設備國產化。包括三星電子(Samsung)、海力士(Hynix)、東部亞南(DongbuAnam)半導體等主要業者及學界、研究機構、政府等單位,也將於2007年正式推動「半導體核心設備開發事業團」。
至於大陸部分,隨著第十一次5年計畫(2006∼2010)的啟動,發展主軸為提高技術層次並擴及半導體材料與設備領域,其次則是新增「積體電路產業促進條例」,根據資訊產業科技發展「十一五」規劃和2020年中長期規劃綱要,半導體技術獎勵政策,初步決定將以12吋廠與0.18微米以下先進製程為主,改變以往全面性的獎勵方式,重點發展項目包括12吋晶圓廠、16吋晶圓廠以及90奈米、65奈米和45奈米製程技術、MEMS技術、新型、高密度積體電路封裝、測試技術。
而在國產化設備部分,獎勵部分則為半導體和積體電路專用設備製造技術(含矽基、化合物、寬禁帶半導體設備製造技術)以及半導體和積體電路測試儀器製造技術,目標是6吋晶圓生產線設備上完全自主,8吋晶圓以及12吋晶圓生產線0.13∼0.065微米微影設備等有所突破。
且新的半導體產業發展政策除對半導體業者採行「五免五減半」的所得稅優惠措施外,另提供業者研發減稅、半導體設備支出免稅,以及協助IC設計業者尋求資金籌措管道等;並計劃成立專案基金扶植半導體產業,第一年基金規模達1,200萬∼2,500萬美元,之後基金規模將逐年擴大。
台灣在半導體產業中佔有不可替代的重要地位,如何利用既有的優勢來帶動半導體次產業(設備、材料等)的興起,是相關廠商以及政府部門所必須重視的。面對南韓強力競爭與大陸半導體產業日益蓬勃發展的威脅,台灣政府部門應該思考如何協助業者能夠創新技術,掌握半導體設備發展,讓不僅晶圓生產技術根留台灣,同時設備方面也能自主,厚植台灣半導體產業基礎技術,補足長久一來,台灣所欠缺的這一塊空白。
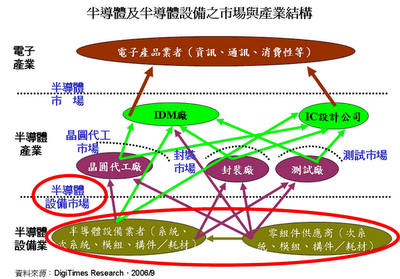
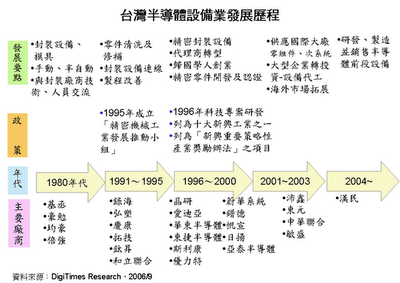
Subscribe to:
Posts (Atom)